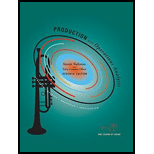
Production and Operations Analysis, Seventh Edition
7th Edition
ISBN: 9781478623069
Author: Steven Nahmias, Tava Lennon Olsen
Publisher: Waveland Press, Inc.
expand_more
expand_more
format_list_bulleted
Concept explainers
Question
Chapter 8.2, Problem 18P
a
Summary Introduction
Interpretation: The optimal production plan and the holding and setup costs are to be calculated.
Concept Introduction: The production level at which the short term profits are maximized, and that at which setup and holding costs are least, is referred to as the optimal production plan.
b
Summary Introduction
Interpretation: The optimal production plan and the holding and setup costs using backward dynamic programming.
Concept Introduction: The production level at which the short term profits are maximized, and that at which setup and holding costs are least, is referred to as the optimal production plan.
Expert Solution & Answer

Want to see the full answer?
Check out a sample textbook solution
Students have asked these similar questions
corrugated
carton
number of units
profit
6
4
0
constraints
cutting
2
3
0
= <
120
pinning
2
1
0
= <
60
LHS
SIGN
RHS
Part B
Step 1: Use the formulated problem as in part A with the return and constraint coefficients to set up Excel sheet
Step 2
Setting up the worksheet
Key in the profit coefficients per box type in range B3:c3
■ key in the LHS constraint coefficients in terms of Decision variables, for example variable "x1" or "b" has a coefficient of 2 is written 2x1 or 2b
using the range B5:C7…
A single inventory item is ordered from an outside supplier. The anticipateddemand for this item over the next 12 months is 6, 12, 4, 8, 15, 25, 20, 5, 10, 20, 5,12. Current inventory of this item is 4, and ending inventory should be 8. Assume aholding cost of $1 per period and a setup cost of $40. Determine the order policyfor this item based ona. Silver–Meal.
Auria will produce 3 vehicle components and knows that each start generates a cost of 5,000 pesos. The cost of the units is $ 200, $ 100 and $ 70 respectively. Annual demand is 100,000 units for Product A, 150,000 units for Product B, and 200,000 units for Product C. The inventory rate is 15% per month. Product A and B are basic and substitutable products, so there must be a minimum average inventory of 8,000 units of both. The company seeks a maximum of $ 100,000 invested money in inventory. The available warehouse space is 400m3 and product A occupies 0.5m3, product B 0.7m3 and C 1m3. Consider that product A and C allow shortages and the goodwill loss cost is $ 3 for each unit of those items.
a) Formulate the problem as a mathematical programming model (objective function and constraints) that minimizes the total annual cost
Chapter 8 Solutions
Production and Operations Analysis, Seventh Edition
Ch. 8.1 - Prob. 1PCh. 8.1 - Prob. 2PCh. 8.1 - Prob. 3PCh. 8.1 - Prob. 4PCh. 8.1 - Prob. 5PCh. 8.1 - Prob. 6PCh. 8.1 - Prob. 7PCh. 8.1 - Prob. 8PCh. 8.1 - Prob. 9PCh. 8.2 - Prob. 10P
Ch. 8.2 - Prob. 11PCh. 8.2 - Prob. 12PCh. 8.2 - Prob. 13PCh. 8.2 - Prob. 14PCh. 8.2 - Prob. 15PCh. 8.2 - Prob. 16PCh. 8.2 - Prob. 17PCh. 8.2 - Prob. 18PCh. 8.2 - Prob. 19PCh. 8.2 - Prob. 20PCh. 8.2 - Prob. 21PCh. 8.2 - Prob. 22PCh. 8.3 - Prob. 23PCh. 8.3 - Prob. 24PCh. 8.3 - Prob. 25PCh. 8.4 - Prob. 26PCh. 8.4 - Prob. 27PCh. 8.4 - Prob. 28PCh. 8.4 - Prob. 29PCh. 8.5 - Prob. 30PCh. 8.5 - Prob. 31PCh. 8.5 - Prob. 32PCh. 8.5 - Prob. 33PCh. 8.5 - Prob. 34PCh. 8.6 - Prob. 35PCh. 8.6 - Prob. 36PCh. 8.6 - Prob. 37PCh. 8.6 - Prob. 38PCh. 8.6 - Prob. 39PCh. 8.6 - Prob. 40PCh. 8 - Prob. 41APCh. 8 - Prob. 42APCh. 8 - Prob. 43APCh. 8 - Prob. 44APCh. 8 - Prob. 45APCh. 8 - Prob. 46APCh. 8 - Prob. 48APCh. 8 - Prob. 49APCh. 8 - Prob. 50APCh. 8 - Prob. 51AP
Knowledge Booster
Learn more about
Need a deep-dive on the concept behind this application? Look no further. Learn more about this topic, operations-management and related others by exploring similar questions and additional content below.Similar questions
- Max the Tailor is going to sell custom suits. He was able to rent a garage from his Uncle Ed for $2,000 a month, which includes utilities, and he already owns the equipment he needs. He anticipates being able to sell his suits for $500 each. The raw materials (fabric, buttons, zippers, thread, etc.) will cost an average of $75 for each suit, and he plans to spend $25 per suit to advertise them. Assuming these are all the costs and revenues, what will be Max’s monthly break-even point in units? Does this seem like a reasonable amount for him to produce and sell every month? Please show your calculations.arrow_forwardA single inventory item is ordered from an outside supplier. The anticipateddemand for this item over the next 12 months is 6, 12, 4, 8, 15, 25, 20, 5, 10, 20, 5,12. Current inventory of this item is 4, and ending inventory should be 8. Assume aholding cost of $1 per period and a setup cost of $40. Determine the order policyfor this item based ond. Which lot-sizing method resulted in the lowest cost for the 12 periods?arrow_forwardWilliams Inc. produces fluorescent lightbulbs for commercial use. The accounting manager isattempting to estimate the total cost for the next quarter using the high-low method. He has compileddata and found the high and low costs are $10,000 and $6,000, respectively, and the associated costdrivers are 7,000 and 3,000 packs, respectively. What is the value for b (the variable cost per unit)?What is the value for a (the fixed quantity)?arrow_forward
- Francesca’s Boutique has a merchandise budget that includes $53,420 in planned sales for Dresses, $5342 in planned reductions, and $63,762 in planned purchases. The assortment includes 4 sub classifications (Casual (30%), dressy (20%), day-to-night (35%), date night (15%)) with 5styles, 4 colors, 4 sizes (for each sub class). The average first price on the dress is $45. Francesca’s expects to devote about 50 square feet to displaying the dresses in each store (10 stores), and the shirts to generate approx. $107 per square foot during the fall selling period. Markdowns are expected to be 10% of sales. Average Markup is 63%. Based on the information provided: What is the planned volume of the assortment? (Note: Use Planned Merchandise to Receive figures) How many SKUs are in this assortment? What is the model stock for the entire dress assortment?arrow_forwardThe table below provides demand data for 6 weeks (weeks 31-36 for the current year) for one product. Inventory is managed with a periodic review system where T = 5 weeks and M = 280. The previous order was for 120 units at the end of week 28. The lead time is a constant 4 weeks. At the beginning of week 31 the inventory level is 130 units. Orders are made at the end of a week. 1. When is the next order? end of week __________ 2. How large is the next order? ___________ Week Demand Inventory 31 30 32 40 33 45 34 30 35 30 36 30arrow_forwardA single inventory item is ordered from an outside supplier. The anticipateddemand for this item over the next 12 months is 6, 12, 4, 8, 15, 25, 20, 5, 10, 20, 5,12. Current inventory of this item is 4, and ending inventory should be 8. Assume aholding cost of $1 per period and a setup cost of $40. Determine the order policyfor this item based onb. Least unit costarrow_forward
- Anticipated demands for a five-period planning horizon are 14, 3, 0, 26, 15. Current starting inventory is four units, and the inventory manager would like to have eight units on hand at the end of the planning horizon. Assume that h = 1 and K = 30. Find the optimal production schedule. (Hint: Modify the first and the last period’s demands to account for starting and ending inventories.)arrow_forwardEconomic production quantity. This type of problem can be recognized when a production rate (p) Problem 2is given in addition to the basic EOQ information. Use Formula 13–5 to compute the optimal runquantity. Production (run) time is Q/p. Imax is (Q/p)(p – u). The time between the end of one run andthe start of the next is (Imax)/u – setup time.The Dine Corporation is both a producer and a user of brass couplings. The firm operates 220days a year and uses the couplings at a steady rate of 50 per day. Couplings can be produced at a rateof 200 per day. Annual storage cost is $2 per coupling, and machine setup cost is $70 per run.a. Determine the economic run quantity.b. Approximately how many runs per year will there be?c. Compute the maximum inventory level.d. What is the average inventory on hand?e. Determine the length of the pure consumption portion of the cyclearrow_forwardLeather-All produces a line of handmade leather products. At the present time, the company is producing only belts, handbags, and attache cases. The predicted demand for these three types of items over a six-month planning horizon is as follows: Month No. of Belts Handbags Attache CasesWorking days1 22 2500 1250 2402 20 2800 680 3803 19 2000 1625 1104 24 3400 745 755 21 3000 835 1266 17 1600 375 45 The belts require an average of two hours to produce, the handbags three hours, and the attache cases six hours; all the workers have the skill to work on any item. Leather-All has 46 employees who each have a share in the firm and cannot be fired. There are an additional 30 locals that are available and can be hired for short periods at a higher cost. Regular employees earn $8.50 per hour on regular time, and $14.00 per hour on overtime. Regular time comprises a seven-hour workday and the regular employees will work as much overtime as is available. The additional workers are hired for…arrow_forward
- Problem 21-9 (Algo) Semans is a manufacturer that produces bracket assemblies. Demand for bracket assemblies (X) is 137 units. The following is the BoM in indented form: ITEM DESCRIPTION USAGE X Bracket assembly 1 A Wall board 5 B Hanger subassembly 2 D Hanger casting 2 E Ceramic knob 1 C Rivet head screw 4 F Metal tong 3 G Plastic cap 1 Below is a table indicating current inventory levels: Item X A B C D E F G Inventory 30 20 73 22 200 149 1,000 90 b. What are the net requirements of each item in the MPS? (Leave no cells blank - be certain to enter "0" wherever required.)arrow_forwardA mail-order house uses 16,870 boxes a year. Carrying costs are 60 cents per box a year, and ordering costs are $96. The following price schedule applies. Number of BoxesPrice per Box1,000 to 1,999$1.25 2,000 to 4,9991.20 5,000 to 9,9991.15 10,000 or more1.10 a.Determine the optimal order quantity. (Round your answer to the nearest whole number.) Optimal order quantity5000 boxes b.Determine the number of orders per year. (Round your answer to 2 decimal places.) Number of order per yeararrow_forwardThe BOMs for products A & B and data from the inventoryrecords are shown in Figure 11.41. Data from the inventoryrecords are shown in Table 11.10. In the MPS for product A,the MPS start row has 85 units in week 2 and 200 in week 4and 50 in week 8. In the MPS for product B, the MPS start rowhas 65 units in week 3 and 50 in week 4 and 50 in week 5 and75 in week 8.a. Develop the material requirements plan for the next8 weeks for items C, D, and E. Note any difficulties youobserve in the inventory records.b. Can the difficulties noted in part (a) be rectified byexpediting any Scheduled Receipts?arrow_forward
arrow_back_ios
SEE MORE QUESTIONS
arrow_forward_ios
Recommended textbooks for you
- Practical Management ScienceOperations ManagementISBN:9781337406659Author:WINSTON, Wayne L.Publisher:Cengage,
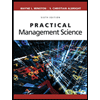
Practical Management Science
Operations Management
ISBN:9781337406659
Author:WINSTON, Wayne L.
Publisher:Cengage,
Inventory Management | Concepts, Examples and Solved Problems; Author: Dr. Bharatendra Rai;https://www.youtube.com/watch?v=2n9NLZTIlz8;License: Standard YouTube License, CC-BY