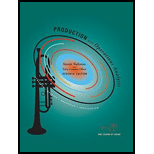
Production and Operations Analysis, Seventh Edition
7th Edition
ISBN: 9781478623069
Author: Steven Nahmias, Tava Lennon Olsen
Publisher: Waveland Press, Inc.
expand_more
expand_more
format_list_bulleted
Concept explainers
Question
Chapter 8.3, Problem 25P
Summary Introduction
Interpretation: The planned order release for component A and B along with resulting gross requirement schedules for component C, D and E are to be determined.
Concept Introduction:
The planned order release can be called as method which is based on the specified lead time till the planned receipt date is not received.
Expert Solution & Answer

Want to see the full answer?
Check out a sample textbook solution
Students have asked these similar questions
The maintenance department in Ranchi Hospital uses 816 cases of liquid cleanser annually. Ordering costs are $12, carrying costs are $4 per case a year, and the new price schedule indicates that orders of less than 50 cases will cost $20 per case, 50 to 79 cases will cost $18 per case, 80 to 99 cases will cost $17 per case, and larger orders will cost $16 per case. Determine the optimal order quantity and the total cost.
The Economic Order Quantity (EOQ) model is a classical model used for controlling inventory and satisfying demand. Costs included in the model are holding cost per unit, ordering cost and the cost of goods ordered. The assumptions for that model are that only a single item is considered, that the entire quantity ordered arrives at one time, that the demand for the item is constant over time, and that no shortages are allowed.
Suppose we relax the first assumption and allow for multiple items that are independent except for a restriction on the amount of space available to store the products. The following model describes this situation:
Let Dj =
annual demand for item j
Cj =
unit cost of item j
Sj =
cost per order placed for item j
i =
inventory carrying charge as a percentage of the cost per unit
W =
the maximum amount of space available for all goods
wj =
space required for item j
The decision variables are Qj, the amount of item j to order. The model is:…
The Economic Order Quantity (EOQ) model is a classical model used for controlling inventory and satisfying demand. Costs included in the model are holding cost per unit, ordering cost and the cost of goods ordered. The assumptions for that model are that only a single item is considered, that the entire quantity ordered arrives at one time, that the demand for the item is constant over time, and that no shortages are allowed.
Suppose we relax the first assumption and allow for multiple items that are independent except for a restriction on the amount of space available to store the products. The following model describes this situation:
Let Dj =
annual demand for item j
Cj =
unit cost of item j
Sj =
cost per order placed for item j
i =
inventory carrying charge as a percentage of the cost per unit
W =
the maximum amount of space available for all goods
wj =
space required for item j
The decision variables are Qj, the amount of item j to order. The model is:
(view…
Chapter 8 Solutions
Production and Operations Analysis, Seventh Edition
Ch. 8.1 - Prob. 1PCh. 8.1 - Prob. 2PCh. 8.1 - Prob. 3PCh. 8.1 - Prob. 4PCh. 8.1 - Prob. 5PCh. 8.1 - Prob. 6PCh. 8.1 - Prob. 7PCh. 8.1 - Prob. 8PCh. 8.1 - Prob. 9PCh. 8.2 - Prob. 10P
Ch. 8.2 - Prob. 11PCh. 8.2 - Prob. 12PCh. 8.2 - Prob. 13PCh. 8.2 - Prob. 14PCh. 8.2 - Prob. 15PCh. 8.2 - Prob. 16PCh. 8.2 - Prob. 17PCh. 8.2 - Prob. 18PCh. 8.2 - Prob. 19PCh. 8.2 - Prob. 20PCh. 8.2 - Prob. 21PCh. 8.2 - Prob. 22PCh. 8.3 - Prob. 23PCh. 8.3 - Prob. 24PCh. 8.3 - Prob. 25PCh. 8.4 - Prob. 26PCh. 8.4 - Prob. 27PCh. 8.4 - Prob. 28PCh. 8.4 - Prob. 29PCh. 8.5 - Prob. 30PCh. 8.5 - Prob. 31PCh. 8.5 - Prob. 32PCh. 8.5 - Prob. 33PCh. 8.5 - Prob. 34PCh. 8.6 - Prob. 35PCh. 8.6 - Prob. 36PCh. 8.6 - Prob. 37PCh. 8.6 - Prob. 38PCh. 8.6 - Prob. 39PCh. 8.6 - Prob. 40PCh. 8 - Prob. 41APCh. 8 - Prob. 42APCh. 8 - Prob. 43APCh. 8 - Prob. 44APCh. 8 - Prob. 45APCh. 8 - Prob. 46APCh. 8 - Prob. 48APCh. 8 - Prob. 49APCh. 8 - Prob. 50APCh. 8 - Prob. 51AP
Knowledge Booster
Learn more about
Need a deep-dive on the concept behind this application? Look no further. Learn more about this topic, operations-management and related others by exploring similar questions and additional content below.Similar questions
- In Lecture 5 we extended the newsvendor solution to the infinite horizon problem when there is no order lead time. Now suppose that the order lead time is L periods throughout the infinite horizon: if an order is placed at the beginning of period t, it arrives at the beginning of period t+L. Can we still extend the newsvendor solution to the infinite horizon problem in the case of backordering? Why or why not? Would your answer change in the case of lost sales? Why or why or not? I WANT LONG AND CLEAR EXPLANATION NOT AN 1 SENTENCE!!!!!!arrow_forwardThe Economic Order Quantity (EOQ) model is a classical model used for controlling inventory and satisfying demand. Costs included in the model are holding cost per unit, ordering cost, and the cost of goods ordered. The assumptions for that model are that only a single item is considered, that the entire quantity ordered arrives at one time, that the demand for the item is constant over time, and that no shortages are allowed. Suppose we relax the first assumption and allow for multiple items that are independent except for a restriction on the amount of space available to store the products. The following model describes this situation: Let Dj = annual demand for item j Cj = unit cost of item j Sj = cost per order placed for item j i = inventory carrying charge as a percentage of the cost per unit W = the maximum amount of space available for all goods wj = space required for item j The decision variables are Qj , the amount of item j to order. The model is: In…arrow_forwardA distribution center (DC) in Wisconsin stocks Sony plasma TV sets. The center receives its inventory from a mega warehouse in Kansas with a lead time (L) of 5 days. The DC uses a reorder point (R) of 300 sets and afixed order quantity (Q) of 250 sets. The current on-hand inventory (OH) at the end of Day 1 is 400 sets, there are no scheduled receipts (SR), and there are no backorders (BO). Assume that all demands and receipts occur at the end of the day. The inventory position is compared to the reorder point after demands and receipts are accounted for. If necessary, an order is placed and the inventory position is updated. Given the demand schedule in the table below, determine when to order using a (Q) systemarrow_forward
- The production order quantity for this problem is approximately 332 units. daily demand rate = 64; daily production rate = 100. What is the average inventory on - hand ( in other words - the inventory for which you are paying Holding Costs ) In this problem ?arrow_forwardThe maintenance department of a large hospital uses 816 cases of liquid cleaner annually. Ordering costs are $12, carrying costs are $4 per case per year, and the new price schedule indicates that orders of less than 50 cases will cost $20 per case, 50 to 79 cases will cost $18 per case, 80 to 99 cases will cost $17 per case, and larger orders will cost $16 per case. Determine the optimal order quantity and the total costarrow_forwardThe maintenance department of a large hospital uses about 816 cases of liquid cleanserannually. Ordering costs are $12, carrying costs are $4 per case a year, and the new priceschedule indicates that orders of less than 50 cases will cost $20 per case, 50 to 79 caseswill cost $18 per case, 80 to 99 cases will cost $17 per case, and larger orders will cost $16per case. Determine the optimal order quantity and the total cost.arrow_forward
- A local outdoor vegetable stand has exactly 1,000 square feet of space to display three vegetables: tomatoes, lettuce, and zucchini. The appropriate data for these items are given in the following table. (given) The setup cost for replenishment of the vegetables is $100 in each case, and the space consumed by each vegetable is proportional to its costs, with tomatoes requiring 0.5 square foot per pound. The annual interest rate used for computing holding costs is 25 percent. What are the optimal quantities that should be purchased of these three vegetables?arrow_forwardConsider that you work at Kroger Grocery store, and that you've been tasked with creating an ABC inventory classification for 6 items. The 6 items, as well as their profit per case and number of cases sold per week, are as follows:Ribeye Steak - $135 in profit per case, 3 cases sold per weekLobster Tail - $245 in profit per case, 3 cases sold per weekPasta - $23 in profit per case, 12 cases sold per weekSalt - $3 in profit per case, 2 cases sold per weekNapkins - $12 in profit per case, 2 cases sold per weekTomato Sauce - $23 in profit per case, 11 cases sold per weekUsing total weekly profits, please classify each products into A, B, or C categories. Which items form the boundary of the class A and B items in your classification, and why? Which items form the boundary of the class B and C items in your classification, and why?arrow_forward[item no. 11] In a single period inventory model, the demand is assumed to follow a normal distribution. The value of ML/(ML+MP) is 0.6. The company used marginal analysis with the normal distribution to determine the optimal stocking level X*. If the mean demand is 100, then X* a. is less than 100 b. is equal to 100 c. cannot be determined from the information given d. is greater than 100arrow_forward
- The Hawkins Supply Company is currently faced with an inventory rotation problem. This difficulty stems from the fact that some supplies must be used prior to a stated expiration date. Upon receipt, a new shipment of these perishable items must be stacked beneath the boxes that are currently in inventory. A substantial amount of time is consumed in restacking the items according to their expiration dates.The company would like to reduce the double and sometimes triple handling of items. How can this goal be achieved? Are there alternative solutions which might also be effective?arrow_forwardAuria will produce 3 vehicle components and knows that each start generates a cost of 5,000 pesos. The cost of the units is $ 200, $ 100 and $ 70 respectively. Annual demand is 100,000 units for Product A, 150,000 units for Product B, and 200,000 units for Product C. The inventory rate is 15% per month. Product A and B are basic and substitutable products, so there must be a minimum average inventory of 8,000 units of both. The company seeks a maximum of $ 100,000 invested money in inventory. The available warehouse space is 400m3 and product A occupies 0.5m3, product B 0.7m3 and C 1m3. Consider that product A and C allow shortages and the goodwill loss cost is $ 3 for each unit of those items. a) Formulate the problem as a mathematical programming model (objective function and constraints) that minimizes the total annual costarrow_forwardRecently, a kiddie store has been given a quantity discount schedule for these cats. Thus, the normal cost for the toy cars is P200.00. For orders betweeen 1,000 and 1,999 units, the unit cost drops to P192.00. For orders of 2,000 or more units, the unit cost is only P190.00. Furthermore, ordering cost is P1,960.00 per order. Annual demand is 5,000 toy cars, and inventory carrying charge, as a percentage of cost, I, is 20%. What order size quantity will minimize the total inventory cost?arrow_forward
arrow_back_ios
SEE MORE QUESTIONS
arrow_forward_ios
Recommended textbooks for you
- Practical Management ScienceOperations ManagementISBN:9781337406659Author:WINSTON, Wayne L.Publisher:Cengage,
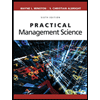
Practical Management Science
Operations Management
ISBN:9781337406659
Author:WINSTON, Wayne L.
Publisher:Cengage,