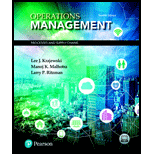
Operations Management: Processes and Supply Chains (12th Edition) (What's New in Operations Management)
12th Edition
ISBN: 9780134741062
Author: Lee J. Krajewski, Manoj K. Malhotra, Larry P. Ritzman
Publisher: PEARSON
expand_more
expand_more
format_list_bulleted
Question
Chapter 5, Problem 9P
Summary Introduction
Interpretation: The product mix for improving the profitability and change in profit needs to be determined.
Concept Introduction: Contribution margin is concerned with preparing income statement. Generally for calculating profit or loss in business it is required.
Expert Solution & Answer

Want to see the full answer?
Check out a sample textbook solution
Students have asked these similar questions
Yost-Perry Industries’ (YPI) senior management team wants to improve the profitability of the firm by accepting the right set of orders. Currently, decisions are made using the traditional method, which is to accept as much of the highest contribution margin product as possible (up to the limit of its demand), followed by the next highest contribution margin product, and so on until all available capacity is utilized. Because the firm cannot satisfy all the demand, the product mix must be chosen carefully. Jay Perry, the newly promoted production supervisor, is knowledgeable about the TOC and the bottleneck-based method for scheduling. He believes that profitability can indeed be improved if bottleneck resourcesare exploited to determine the product mix. What is the change in profits if, instead of the traditional method that YPI has used thus far, the bottleneck method advocated by Jay is used for selecting the product mix?
The Build-Em-Fast Company has agreed to supply its best customer with three widgets during each of the next 3 weeks, even though producing them will require some overtime work. The relevant production data are as follows:
Week
Maximum Production,
Regular Time
Maximum Production,
Overtime
Production Cost per Unit,
Regular Time
1
2
2
$300
2
3
2
$500
3
1
2
$400
The cost per unit produced with overtime for each week is $100 more than for regular time. The cost of storage is $50 per unit for each week it is stored. There is already an inventory of two widgets on hand currently, but the company does not want to retain any widgets in inventory after the 3 weeks.
Management wants to know how many units should be produced in each week to minimize the total cost of meeting the delivery schedule.
Formulate this problem as a transportation problem by constructing the appropriate parameter table.
A.J.’s Wildlife Emporium manufactures two unique birdfeeders (Deluxe and Super Duper) that are manufactured and assembled in up to three different workstations (X, Y, Z) using a small batch process. Each of the products is produced according to the flowchart in Figure. Additionally, the flowchart indicates each product’s price, weekly demand, and processing times per unit. Batch setup times are negligible.A.J. can make and sell up to the limit of its weekly demand and there are no penalties for not being able to meet all of the demand. Each workstation is staffed by a worker who is dedicated to work on that workstation alone and is paid $16 per hour. The plant operates 40 hours per week, with no overtime. Overhead costs are $2,000 per week. Based on the information provided, as well as the information contained in the flowchart, answer the following questions. a. Using the traditional method, which bases decisions solely on a product’s contribution to profits and overhead, what is the…
Chapter 5 Solutions
Operations Management: Processes and Supply Chains (12th Edition) (What's New in Operations Management)
Ch. 5 - Take a process that you encounter on a daily...Ch. 5 - Prob. 2DQCh. 5 - How could the efficiency of the redesigned process...Ch. 5 - Bill’s Barbershop has two barbers available to...Ch. 5 - Melissa’s Photo Studio offers both individual...Ch. 5 - Figure 5.11 details the process flow for two types...Ch. 5 - Prob. 4PCh. 5 - Super Fun Industries manufactures four top-selling...Ch. 5 - Prob. 6PCh. 5 - Yost-Perry Industries (YPI) manufactures a mix of...
Ch. 5 - Prob. 8PCh. 5 - Prob. 9PCh. 5 - A.J.’s Wildlife Emporium manufactures two unique...Ch. 5 - Cooper River Glass Works (RGW) produces four...Ch. 5 - Quick Stop Pharmacy is a small family-owned,...Ch. 5 - Use the longest work element rule to balance the...Ch. 5 - Johnson Cogs wants to set up a line to serve 60...Ch. 5 - Refer back to Problem 16. Suppose that in addition...Ch. 5 - To meet holiday demand, Penny’s Pie Shop...Ch. 5 - A paced assembly line has been devised to...Ch. 5 - Prob. 20PCh. 5 - Greg Davis, a business major at the University of...Ch. 5 - Prob. 1VCCh. 5 - Which boarding scenario among the different ones...Ch. 5 - How should Southwest evaluate the gate boarding...Ch. 5 - How will Southwest know that the bottleneck had...
Knowledge Booster
Similar questions
- For the four basic configurations that follow, assume that the market is demanding product that must be processed by both Resource X and Resource Y for Cases I, II, and III. For Case IV, both resources supply separate but dependent markets; that is, the number of units of output from both X and Y must be equal. Plans are being made to produce a product that requires 40 minutes on Resource X and 30 minutes on Resource Y. Assume that there is only one of each of these resources and that market demand is 1,500 units per month. The only one I got right was B Case I :(arrow_forwardTailwind, Inc., produces high-quality but expensive training shoes for nmners. The Tailwind shoe, which sells for $210, contains both gas- and liquid-filled compartments to provide morestability and better protection against knee, foot, and back injuries. Manufacturing the shoes requires 10 separate tasks. There are 400 minutes available for manufacturing the shoes in the plant each day. Daily demand is 60. The information for the tasks is as follows: a) Draw the precedence diagram.b) Assign tasks to thl e minimum feasible number of workstations according to the "ranked positioned weight" decision rule.c) What is the efficiency of the process you completed in (b)?d) What is the idle time per cycle?arrow_forwardThe senior management at Best Products Company (BPC) is concerned with the existing capacity limitation, so they want to accept the mix of orders that maximizes the company’s profits. Traditionally, BPC has utilized a method whereby decisions are made to produce as much of the product with the highest contribution margin as possible (up to the limit of its demand), followed by the next highest contribution margin product, and so on until no more capacity is available. Because capacity is limited, choosing the proper product mix is crucial. Ali Ahmed, the newly hired production supervisor, is an avid follower of the theory of constraints philosophy and the bottleneck method for scheduling. He believes that profitability can indeed be approved if bottleneck resources are exploited to determine the product mix. What is the profit if the traditional contribution margin method is used for determining BPC’s product mix?arrow_forward
- 2-The process of making hotdogs involves six activities: “grind”, “mix”, “stuff”, “cook”, “peel”, and “inspect”. If the capacity of activity “cook” determines the process capacity, which of the following statements are true? a- Activity “cook” is a bottleneck activity. b- The activity time of all the other five activities is shorter than activity "cook". c- Cycle time of the process of making hotdogs is equal=1/capacity of activity “cook”. d- Increasing the capacity of activity “grind” can increase the capacity of the process of making hotdogs. All statements are correct Only statement 'b' is correct Only statements 'a' and 'b' are correct Only statements 'a', 'b' and 'c' are correct Only statement 'a' is correct Only statement 'd' is correctarrow_forwardGeorgetown Pizza makes its favorite pan pizzas every day with three working shifts around the clock. The current completely cooked pizza-making process has a fixed cost of $24,000, and a variable cost of $2.75 per pizza. The owner is considering a different process that can make pizzas in two ways: completely cooked and selling at $13.98 per unit, or partially cooked with a selling price of $12.98 per unit. This alternate process has a fixed cost of $28,000, but a lower variable cost (because much less energy is used in baking) of $2.25 per pizza. a. Determine the breakeven quantity between the current pizza-making process and the alternate process.arrow_forwardA linear programming computer package is needed. EZ-Windows, Inc., manufactures replacement windows for the home remodeling business. In January, the company produced 15,000 windows and ended the month with 9,000 windows in inventory. EZ-Windows' management team would like to develop a production schedule for the next three months. A smooth production schedule is obviously desirable because it maintains the current workforce and provides a similar month-to-month operation. However, given the sales forecasts, the production capacities, and the storage capabilities as shown, the management team does not think a smooth production schedule with the same production quantity each month possible. February March April Sales forecast 15,000 16,500 20,000 Production capacity 14,000 14,000 18,000 Storage capacity 6,000 6,000 6,000 The company's cost accounting department estimates that increasing production by one window from one month to the next will increase total costs by $1.00…arrow_forward
- A linear programming computer package is needed. EZ-Windows, Inc., manufactures replacement windows for the home remodeling business. In January, the company produced 15,000 windows and ended the month with 9,000 windows in inventory. EZ-Windows' management team would like to develop a production schedule for the next three months. A smooth production schedule is obviously desirable because it maintains the current workforce and provides a similar month-to-month operation. However, given the sales forecasts, the production capacities, and the storage capabilities as shown, the management team does not think a smooth production schedule with the same production quantity each month possible. February March April Sales forecast 15,000 16,500 20,000 Production capacity 14,000 14,000 18,000 Storage capacity 6,000 6,000 6,000 The company's cost accounting department estimates that increasing production by one window from one month to the next will increase total costs by $1.00…arrow_forwardA linear programming computer package is needed. EZ-Windows, Inc., manufactures replacement windows for the home remodeling business. In January, the company produced 15,000 windows and ended the month with 9,000 windows in inventory. EZ-Windows' management team would like to develop a production schedule for the next three months. A smooth production schedule is obviously desirable because it maintains the current workforce and provides a similar month-to-month operation. However, given the sales forecasts, the production capacities, and the storage capabilities as shown, the management team does not think a smooth production schedule with the same production quantity each month possible. February March April Sales forecast 15,000 16,500 20,000 Production capacity 14,000 14,000 18,000 Storage capacity 6,000 6,000 6,000 The company's cost accounting department estimates that increasing production by one window from one month to the next will increase total costs by $1.00…arrow_forwardExplain and expand these importance of capacity planning. 1. Capacity decisions have a real impact on the ability of the organization to meet future demands for products and services. 2. Capacity decisions affect operating costs. 3. Capacity is usually a major determinant of initial cost. Typically, the greater the capacity of a productive unit, the greater its cost.arrow_forward
- A manager must decide which type of machine to buy, A, B, or C. Machines costs are as follows: Machine Cost A $40,000 B $30,000 C $80,000 Product forecast, processing times on the machines, and setup times are as follows: Processing Time Per Unit (minutes) Product Annual Demand A B C Setup Times (minutes) Production Lots (units) 1 16,000 3 4 2 20 200 2 12,000 4 5 3 35 100 3 6,000 5 6 3 60 50 4 30,000 2 4 1 15 500 Machines operate 10 hours a day, 250 days a year. The manager wants to have a capacity cushion of 10%. a. Assume that only purchasing costs are being considered. Which machines would have the lowest total cost, and how many of that machines would be needed? b. Consider this additional information: The machines differ in terms of hourly operating costs: The A machines have an hourly operating cost of $11 each, B machines have an hourly operating cost of $10 each, and C machines have an hourly operating cost of $12 each. Which alternative would…arrow_forwardColeman Rich, Ltd., has received the followingorders:Period 1 2 3 4 5 6 7 8 9 10Order size 60 30 10 40 70 10 40 30 40 0The entire fabrication for these units is scheduled on one machine.There are 2,250 usable minutes in a week, and each unit will take 65 minutes to complete. Develop a capacity plan, using lot split-ting, for the 10-week time period.arrow_forwardColonial Furniture produces hand-crafted colonial style furniture. Plans are now being made for the production of rocking chairs, dining room tables, and/or armoires for the next week. These products go through two stages of production (assembly and finishing). The following table gives the time required for each item to go through these two stages, the amount of wood required, and the corresponding unit profits, along with the amount of each resource available next week. Rocking Chair (RC) Dining Room Table (DRT) Armoire(ARM) Available Assembly (minutes) 100 180 120 3,600 Finishing (minutes) 60 80 80 2,000 Wood (pounds) 30 180 120 4,000 Unit Profit $240 $720 $600 Formulate a complete linear programming model that would determine the production levels that would maximize profit. Make sure to identify the decision variables, objective function and constraints. Using Excel’s Solver: what is the optimal solution? In…arrow_forward
arrow_back_ios
SEE MORE QUESTIONS
arrow_forward_ios
Recommended textbooks for you
- Practical Management ScienceOperations ManagementISBN:9781337406659Author:WINSTON, Wayne L.Publisher:Cengage,
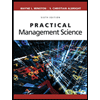
Practical Management Science
Operations Management
ISBN:9781337406659
Author:WINSTON, Wayne L.
Publisher:Cengage,