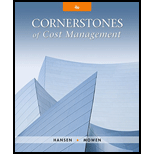
Concept explainers
Leather Works is a family-owned maker of leather travel bags and briefcases located in the northeastern part of the United States. Foreign competition has forced its owner, Heather Gray, to explore new ways to meet the competition. One of her cousins, Wallace Hayes, who recently graduated from college with a major in accounting, told her about the use of cost
In May of last year, Heather asked Matt Jones, chief accountant, and Alfred Prudest, production manager, to implement a
Recently, the following dialogue took place among Heather, Matt, and Alfred:
HEATHER: How is the business performing?
ALFRED: You know, we are producing a lot more than we used to, thanks to the contract that you helped obtain from Lean, Inc., for laptop covers. (Lean is a national supplier of computer accessories.)
MATT: Thank goodness for that new product. It has kept us from sinking even more due to the inroads into our business made by those foreign suppliers of leather goods.
HEATHER: What about the standard costing system?
MATT: The variances are mostly favorable, except for the first few months when the supplier of leather started charging more.
HEATHER: How did the union members take to the standards?
ALFRED: Not bad. They grumbled a bit at first, but they have taken it in stride. We’ve consistently shown favorable direct labor efficiency variances and direct materials usage variances. The direct labor rate variance has been flat.
MATT: It should be since direct labor rates are negotiated by the union representative at the start of the year and remain the same for the entire year.
HEATHER: Matt, would you send me the variance report for laptop covers immediately?
The following chart summarizes the direct materials and direct labor variances from November of last year through April of this year (extracted from the report provided by Matt). Standards for each laptop cover are as follows:
- a. Three feet of direct materials at $7.50 per foot
- b. Forty-five minutes of direct labor at $14 per hour
In addition, the data for May of this year, but not the variances for the month, are as follows:
Actual direct labor cost per hour exceeded the budgeted rate by $0.10 per hour.
Required:
- 1. For May of this year, calculate the price and quantity variances for direct labor and direct materials.
- 2. Discuss the trend of the direct materials and labor variances.
- 3. What type of actions must the workers have taken during the period they were being observed for the setting of standards?
- 4. What can be done to ensure that the standards are set correctly? (CMA adapted)

Trending nowThis is a popular solution!

Chapter 9 Solutions
Cornerstones of Cost Management (Cornerstones Series)
- Quincy Farms is a producer of items made from farm products that are distributed to supermarkets. For many years, Quincys products have had strong regional sales on the basis of brand recognition. However, other companies have been marketing similar products in the area, and price competition has become increasingly important. Doug Gilbert, the companys controller, is planning to implement a standard costing system for Quincy and has gathered considerable information from his coworkers on production and direct materials requirements for Quincys products. Doug believes that the use of standard costing will allow Quincy to improve cost control and make better operating decisions. Quincys most popular product is strawberry jam. The jam is produced in 10-gallon batches, and each batch requires six quarts of good strawberries. The fresh strawberries are sorted by hand before entering the production process. Because of imperfections in the strawberries and spoilage, one quart of strawberries is discarded for every four quarts of acceptable berries. Three minutes is the standard direct labor time required for sorting strawberries in order to obtain one quart of strawberries. The acceptable strawberries are then processed with the other ingredients: processing requires 12 minutes of direct labor time per batch. After processing, the jam is packaged in quart containers. Doug has gathered the following information from Joe Adams, Quincys cost accountant, relative to processing the strawberry jam. a. Quincy purchases strawberries at a cost of 0.80 per quart. All other ingredients cost a total of 0.45 per gallon. b. Direct labor is paid at the rate of 9.00 per hour. c. The total cost of direct material and direct labor required to package the jam is 0.38 per quart. Joe has a friend who owns a strawberry farm that has been losing money in recent years. Because of good crops, there has been an oversupply of strawberries, and prices have dropped to 0.50 per quart. Joe has arranged for Quincy to purchase strawberries from his friends farm in hopes that the 0.80 per quart will put his friends farm in the black. Required: 1. Discuss which coworkers Doug probably consulted to set standards. What factors should Doug consider in establishing the standards for direct materials and direct labor? 2. Develop the standard cost sheet for the prime costs of a 10-gallon batch of strawberry jam. 3. Citing the specific standards of the IMA Statement of Ethical Professional Practice described in Chapter 1, explain why Joes behavior regarding the cost information provided to Doug is unethical. (CMA adapted)arrow_forwardAt the beginning of the last quarter of 20x1, Youngston, Inc., a consumer products firm, hired Maria Carrillo to take over one of its divisions. The division manufactured small home appliances and was struggling to survive in a very competitive market. Maria immediately requested a projected income statement for 20x1. In response, the controller provided the following statement: After some investigation, Maria soon realized that the products being produced had a serious problem with quality. She once again requested a special study by the controllers office to supply a report on the level of quality costs. By the middle of November, Maria received the following report from the controller: Maria was surprised at the level of quality costs. They represented 30 percent of sales, which was certainly excessive. She knew that the division had to produce high-quality products to survive. The number of defective units produced needed to be reduced dramatically. Thus, Maria decided to pursue a quality-driven turnaround strategy. Revenue growth and cost reduction could both be achieved if quality could be improved. By growing revenues and decreasing costs, profitability could be increased. After meeting with the managers of production, marketing, purchasing, and human resources, Maria made the following decisions, effective immediately (end of November 20x1): a. More will be invested in employee training. Workers will be trained to detect quality problems and empowered to make improvements. Workers will be allowed a bonus of 10 percent of any cost savings produced by their suggested improvements. b. Two design engineers will be hired immediately, with expectations of hiring one or two more within a year. These engineers will be in charge of redesigning processes and products with the objective of improving quality. They will also be given the responsibility of working with selected suppliers to help improve the quality of their products and processes. Design engineers were considered a strategic necessity. c. Implement a new process: evaluation and selection of suppliers. This new process has the objective of selecting a group of suppliers that are willing and capable of providing nondefective components. d. Effective immediately, the division will begin inspecting purchased components. According to production, many of the quality problems are caused by defective components purchased from outside suppliers. Incoming inspection is viewed as a transitional activity. Once the division has developed a group of suppliers capable of delivering nondefective components, this activity will be eliminated. e. Within three years, the goal is to produce products with a defect rate less than 0.10 percent. By reducing the defect rate to this level, marketing is confident that market share will increase by at least 50 percent (as a consequence of increased customer satisfaction). Products with better quality will help establish an improved product image and reputation, allowing the division to capture new customers and increase market share. f. Accounting will be given the charge to install a quality information reporting system. Daily reports on operational quality data (e.g., percentage of defective units), weekly updates of trend graphs (posted throughout the division), and quarterly cost reports are the types of information required. g. To help direct the improvements in quality activities, kaizen costing is to be implemented. For example, for the year 20x1, a kaizen standard of 6 percent of the selling price per unit was set for rework costs, a 25 percent reduction from the current actual cost. To ensure that the quality improvements were directed and translated into concrete financial outcomes, Maria also began to implement a Balanced Scorecard for the division. By the end of 20x2, progress was being made. Sales had increased to 26,000,000, and the kaizen improvements were meeting or beating expectations. For example, rework costs had dropped to 1,500,000. At the end of 20x3, two years after the turnaround quality strategy was implemented, Maria received the following quality cost report: Maria also received an income statement for 20x3: Maria was pleased with the outcomes. Revenues had grown, and costs had been reduced by at least as much as she had projected for the two-year period. Growth next year should be even greater as she was beginning to observe a favorable effect from the higher-quality products. Also, further quality cost reductions should materialize as incoming inspections were showing much higher-quality purchased components. Required: 1. Identify the strategic objectives, classified by the Balanced Scorecard perspective. Next, suggest measures for each objective. 2. Using the results from Requirement 1, describe Marias strategy using a series of if-then statements. Next, prepare a strategy map. 3. Explain how you would evaluate the success of the quality-driven turnaround strategy. What additional information would you like to have for this evaluation? 4. Explain why Maria felt that the Balanced Scorecard would increase the likelihood that the turnaround strategy would actually produce good financial outcomes. 5. Advise Maria on how to encourage her employees to align their actions and behavior with the turnaround strategy.arrow_forwardAs CEO of Riverside Marine, Rachel Moore knows it is important to control costs and to respond quickly to changes in the highly competitive boat-building industry. When Gerbig Consulting proposes that Riverside Marine invest in an ERP system, she forms a team to evaluate the proposal: the plant engineer, the plant foreman, the systems specialist, the human resources director, the marketing director, and the management accountant. A month later, the management accountant Miles Cobalt reports that the team and Gerbig estimate that if Riverside Marine implements the ERP system, it will incur the following costs: Costs of the Project a.$390,000 in software costs b. $85,000 to customize the ERP software and load Riverside Marine'sdata into the new ERP system c. $112,000 for employee training Benefits of the Project a. More efficient order processing should lead to savings of $185,000. b. Streamlining the manufacturing process so that it maps into the ERP…arrow_forward
- Paul Golding and his wife, Nancy, established Crunchy Chips in 1938. Over the past 60 years, the company has established distribution channels in 11 western states, with production facilities in Utah, New Mexico, and Colorado. In 1980, Pauls son, Edward, took control of the business. By 2017, it was clear that the companys plants needed to gain better control over production costs to stay competitive. Edward hired a consultant to install a standard costing system. To help the consultant establish the necessary standards, Edward sent her the following memo: The manufacturing process for potato chips begins when the potatoes are placed into a large vat in which they are automatically washed. After washing, the potatoes flow directly to an automatic peeler. The peeled potatoes then pass by inspectors, who manually cut out deep eyes or other blemishes. After inspection, the potatoes are automatically sliced and dropped into the cooking oil. The frying process is closely monitored by an employee. After the chips are cooked, they pass under a salting device and then pass by more inspectors, who sort out the unacceptable finished chips (those that are discolored or too small). The chips then continue on the conveyor belt to a bagging machine that bags them in 1-pound bags. After bagging, the bags are placed in a box and shipped. The box holds 15 bags. The raw potato pieces (eyes and blemishes), peelings, and rejected finished chips are sold to animal feed producers for 0.16 per pound. The company uses this revenue to reduce the cost of potatoes. We would like this reflected in the price standard relating to potatoes. Crunchy Chips purchases high-quality potatoes at a cost of 0.245 per pound. Each potato averages 4.25 ounces. Under efficient operating conditions, it takes four potatoes to produce one 16-ounce bag of plain chips. Although we label bags as containing 16 ounces, we actually place 16.3 ounces in each bag. We plan to continue this policy to ensure customer satisfaction. In addition to potatoes, other raw materials are the cooking oil, salt, bags, and boxes. Cooking oil costs 0.04 per ounce, and we use 3.3 ounces of oil per bag of chips. The cost of salt is so small that we add it to overhead. Bags cost 0.11 each and boxes 0.52 each. Our plant produces 8.8 million bags of chips per year. A recent engineering study revealed that we would need the following direct labor hours to produce this quantity if our plant operates at peak efficiency: Im not sure that we can achieve the level of efficiency advocated by the study. In my opinion, the plant is operating efficiently for the level of output indicated if the hours allowed are about 10% higher. The hourly labor rates agreed upon with the union are: Overhead is applied on the basis of direct labor dollars. We have found that variable overhead averages about 116% of our direct labor cost. Our fixed overhead is budgeted at 1,135,216 for the coming year. Required: 1. Discuss the benefits of a standard costing system for Crunchy Chips. 2. Discuss the presidents concern about using the result of the engineering study to set the labor standards. What standard would you recommend? 3. Form a group with two or three other students. Develop a standard cost sheet for Crunchy Chips plain potato chips. Round all computations to four decimal places. 4. Suppose that the level of production was 8.8 million bags of potato chips for the year as planned. If 9.5 million pounds of potatoes were used, compute the materials usage variance for potatoes.arrow_forwardIngles Corporation is a manufacturer of tables sold to schools, restaurants, hotels, and other institutions. The table tops are manufactured by Ingles, but the table legs are purchased from an outside supplier. The Assembly Department takes a manufactured table top and attaches the four purchased table legs. It takes 16 minutes of labor to assemble a table. The company follows a policy of producing enough tables to ensure that 40 percent of next months sales are in the finished goods inventory. Ingles also purchases sufficient materials to ensure that materials inventory is 60 percent of the following months scheduled production. Ingless sales budget in units for the next quarter is as follows: Ingless ending inventories in units for July 31 are as follows: Required: 1. Calculate the number of tables to be produced during August. 2. Disregarding your response to Requirement 1, assume the required production units for August and September are 2,100 and 1,900, respectively, and the July 31 materials inventory is 4,000 units. Compute the number of table legs to be purchased in August. 3. Assume that Ingles Corporation will produce 2,340 units in September. How many employees will be required for the Assembly Department in September? (Fractional employees are acceptable since employees can be hired on a part-time basis. Assume a 40-hour week and a 4-week month.) (CMA adapted)arrow_forwardMoisha is developing material standards for her company. The operations manager wants grade A widgets because they are the easiest to work with and are the quality the customers want. Grade B will not work because customers do not want the lower grade, and it takes more time to assemble the product than with grade A materials. Moisha calls several suppliers to get prices for the widget. All are within $0.05 of each other. Since they will use millions of widgets, she decides that the $0.05 difference is important. The supplier who has the lowest price is known for delivering late and low-quality materials. Moisha decides to use the supplier who is $0.02 more but delivers on time and at the right quality. This supplier charges $0.48 per widget. Each unit of product requires four widgets. What is the standard cost per unit for widgets?arrow_forward
- Big Mikes, a large hardware store, has gathered data on its overhead activities and associated costs for the past 10 months. Nizam Sanjay, a member of the controllers department, believes that overhead activities and costs should be classified into groups that have the same driver. He has decided that unloading incoming goods, counting goods, and inspecting goods can be grouped together as a more general receiving activity, since these three activities are all driven by the number of receiving orders. The 10 months of data shown below have been gathered for the receiving activity. Required: 1. Prepare a scattergraph, plotting the receiving costs against the number of purchase orders. Use the vertical axis for costs and the horizontal axis for orders. 2. Select two points that make the best fit, and compute a cost formula for receiving costs. 3. Using the high-low method, prepare a cost formula for the receiving activity. 4. Using the method of least squares, prepare a cost formula for the receiving activity. What is the coefficient of determination?arrow_forwardTonya Martin, CMA and controller or the Parts Division of Gunderson Inc., was meeting with Doug Adams, manager of the division. The topic of discussion was the assignment of overhead costs to jobs and their impact on the divisions pricing decisions. Their conversation was as follows: Tonya: Doug, as you know, about 25% of our business is based on government contracts, with the other 75% based on jobs from private sources won through bidding. During the last several years, our private business has declined. We have been losing more bids than usual. After some careful investigation, I have concluded that we are overpricing some jobs because of improper assignment of overhead costs. Some jobs are also being underpriced. Unfortunately, the jobs being overpriced are coming from our higher-volume, labor-intensive products, so we are losing business. Dong: I think I understand. Jobs associated with our high-volume products are being assigned more overhead than they should be receiving. Then when we add our standard 40% markup, we end up with a higher price than our competitors, who assign costs more accurately. Tonya: Exactly. We have two producing departments, one labor-intensive and the other machine-intensive. The labor-intensive department generates much less overhead than the machine-intensive department. Furthermore, virtually all of our high-volume jobs are labor-intensive. We have been using a plantwide rate based on direct labor hours to assign overhead to all jobs. As a result, the high-volume, labor-intensive jobs receive a greater share of the machine-intensive departments overhead than they deserve. This problem can be greatly alleviated by switching to departmental overhead rates. For example, an average high-volume job would be assigned 100,000 of overhead using a plantwide rate and only 70,000 using departmental rates. The change would lower our bidding price on high-volume jobs by an average of 42,000 per job. By increasing the accuracy of our product costing, we can make better pricing decisions and win back much of our private-sector business. Doug: Sounds good. When can you implement the change in overhead rates? Tonya: It wont take long. I can have the new system working within four to six weekscertainly by the start of the new fiscal year. Doug: Hold it. I just thought of a possible complication. As I recall, most of our government contract work is done in the labor-intensive department. This new overhead assignment scheme will push down the cost on the government jobs, and we will lose revenues. They pay us full cost plus our standard markup. This business is not threatened by our current costing procedures, but we cant switch our rates for only the private business. Government auditors would question the lack of consistency in our costing procedures. Tonya: You do have a point. I thought of this issue also. According to my estimates, we will gain more revenues from the private sector than we will lose from our government contracts. Besides, the costs of our government jobs are distorted. In effect, we are overcharging the government. Doug: They dont know that and never would unless we switch our overhead assignment procedures. I think I have the solution. Officially, lets keep our plantwide overhead rate. All of the official records will reflect this overhead costing approach for both our private and government business. Unofficially. I want you to develop a separate set of books that can be used to generate the information we need to prepare competitive bids for our private-sector business. Required: 1. Do you believe that the solution proposed by Doug is ethical? Explain. 2. Suppose that Tonya decides that Dougs solution is not right and objects strongly. Further suppose that, despite Tonyas objections, Doug insists strongly on implementing the action. What should Tonya do?arrow_forwardJohn Biggs and Patty Jorgenson are both cost accounting managers for a manufacturing division. During lunch yesterday, Patty told John that she was planning on quitting her job in three months because she had accepted a position as controller of a small company in a neighboring state. The starting date was timed to coincide with the retirement of the current controller. Patty was excited because it allowed her to live near her family. Today, the divisional controller took John to lunch and informed him that he was taking a position at headquarters and that he had recommended that Patty be promoted to his position. He indicated to John that it was a close call between him and Patty and that he wanted to let John know personally about the decision before it was announced officially. Required: What should John do? Describe how you would deal with his ethical dilemma (considering the IMA code of ethics in your response).arrow_forward
- Jackie Iverson was furious. She was about ready to fire Tom Rich, her purchasing agent. Just a month ago, she had given him a salary increase and a bonus for his performance. She had been especially pleased with his ability to meet or beat the price standards. But now, she found out that it was because of a huge purchase of raw materials. It would take months to use that inventory, and there was hardly space to store it. In the meantime, space had to be found for the other materials supplies that would be ordered and processed on a regular basis. Additionally, it was a lot of capital to tie up in inventorymoney that could have been used to help finance the cash needs of the new product just coming online. Her interview with Tom was frustrating. He was defensive, arguing that he thought she wanted those standards met and that the means were not that important. He also pointed out that quantity purchases were the only way to meet the price standards. Otherwise, an unfavorable variance would have been realized. Required: 1. CONCEPTUAL CONNECTION Why did Tom Rich purchase the large quantity of raw materials? Do you think that this behavior was the objective of the price standard? If not, what is the objective(s)? 2. CONCEPTUAL CONNECTION Suppose that Tom is right and that the only way to meet the price standards is through the use of quantity discounts. Also, assume that using quantity discounts is not a desirable practice for this company. What would you do to solve this dilemma? 3. CONCEPTUAL CONNECTION Should Tom be fired? Explain.arrow_forwardDeMarco Company is developing a cost formula for its packing activity. Discussion with the workers in the Packing Department has revealed that packing costs are associated with the number of customer orders, the size of the orders, and the relative fragility of the items (more fragile items must be specially wrapped in bubble wrap and Styrofoam). Data for the past 20 months have been gathered: Required: 1. Using the method of least squares, run a regression using the number of orders as the independent variable. 2. Run a multiple regression using three independent variables: the number of orders, the weight of orders, and the number of fragile items. Which regression equation is better? Why? 3. Predict the total packing cost for 25,000 orders, weighing 40,000 pounds, with 4,000 fragile items.arrow_forwardRandy Harris, controller, has been given the charge to implement an advanced cost management system. As part of this process, he needs to identify activity drivers for the activities of the firm. During the past four months, Randy has spent considerable effort identifying activities, their associated costs, and possible drivers for the activities costs. Initially, Randy made his selections based on his own judgment using his experience and input from employees who perform the activities. Later, he used regression analysis to confirm his judgment. Randy prefers to use one driver per activity, provided that an R2 of at least 80 percent can be produced. Otherwise, multiple drivers will be used, based on evidence provided by multiple regression analysis. For example, the activity of inspecting finished goods produced an R2 of less than 80 percent for any single activity driver. Randy believes, however, that a satisfactory cost formula can be developed using two activity drivers: the number of batches and the number of inspection hours. Data collected for a 14-month period are as follows: Required: 1. Calculate the cost formula for inspection costs using the two drivers, inspection hours and number of batches. Are both activity drivers useful? What does the R2 indicate about the formula? 2. Using the formula developed in Requirement 1, calculate the inspection cost when 300 inspection hours are used and 30 batches are produced. Prepare a 90 percent confidence interval for this prediction.arrow_forward
- Cornerstones of Cost Management (Cornerstones Ser...AccountingISBN:9781305970663Author:Don R. Hansen, Maryanne M. MowenPublisher:Cengage LearningPrinciples of Accounting Volume 2AccountingISBN:9781947172609Author:OpenStaxPublisher:OpenStax College
- Managerial Accounting: The Cornerstone of Busines...AccountingISBN:9781337115773Author:Maryanne M. Mowen, Don R. Hansen, Dan L. HeitgerPublisher:Cengage Learning
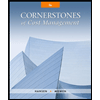
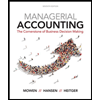